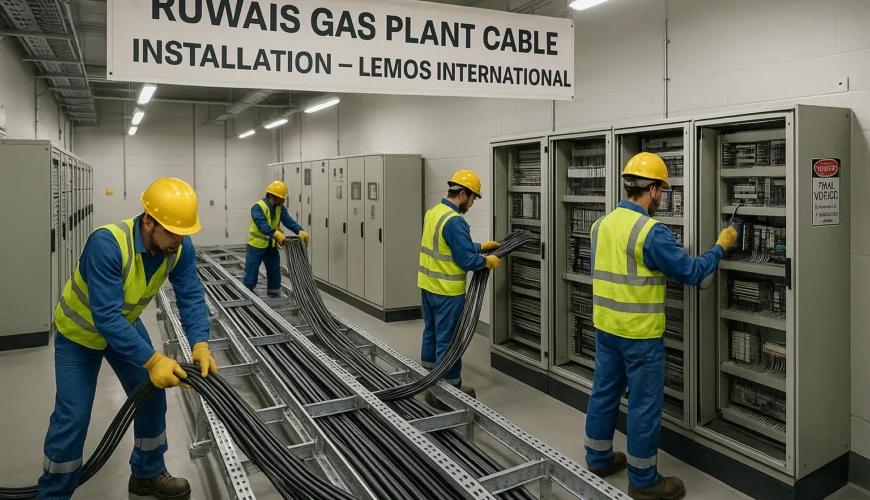
Project Details
- Ruwais Gas Plant
- 24th March 2022
- GASCO – Ruwais
- Cable Tray Installation, Wiring, MCC Commissioning, Control Systems
Project Description
Lemos International successfully executed the installation of cable trays and wiring for the compressor control systems at the Ruwais Gas Plant, operated by GASCO. The project involved the installation of 12 kilometers of multicore control cables, termination and testing of loops to marshalling panels, and commissioning of Motor Control Center (MCC) panels. Our meticulous planning and execution ensured that all systems were energized on time and passed rigorous inspections with flying colors.
Our scope of work included:
- Cable Tray Installation: Designed and installed cable tray systems to support the extensive network of multicore control cables.
- Wiring Execution: Installed and terminated 12km of multicore control cables, ensuring accurate connections to field devices and marshalling panels.
- Loop Testing: Conducted comprehensive loop testing to verify signal integrity and functionality between field instruments and control systems.
- MCC Panel Commissioning: Commissioned MCC panels to ensure seamless integration with the plant’s electrical and control infrastructure.
- QA/QC Compliance: Performed rigorous quality checks and documentation to meet GASCO’s stringent standards.
The project was completed with precision, adhering to international standards and delivering a reliable, efficient, and compliant solution for the gas plant.
Key Features of the Project
Extensive Cable Tray Network
- Designed and installed robust cable tray systems capable of supporting 12km of multicore control cables.
- Ensured proper alignment, spacing, and grounding of trays to prevent signal interference and ensure long-term durability.
Multicore Cable Installation
- Laid and terminated 12km of multicore control cables, connecting field devices such as sensors, transmitters, and actuators to marshalling panels.
- Employed skilled technicians trained in cable pulling, routing, and termination to ensure accuracy and reliability.
Precision Loop Testing
- Conducted detailed loop testing using advanced diagnostic tools to verify signal transmission and system functionality.
- Documented test results meticulously, ensuring traceability and compliance with regulatory requirements.
MCC Panel Commissioning
- Commissioned MCC panels to integrate motor controls with the plant’s Distributed Control System (DCS), enabling centralized monitoring and operation.
- Verified panel performance through functional tests and load simulations to ensure operational readiness.
On-Time Energization
- Successfully energized all systems within the agreed timeline, allowing GASCO to proceed with plant operations without delays.
- Passed all inspections with zero non-conformities, reflecting our commitment to quality and precision.
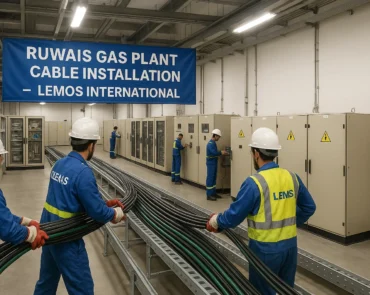
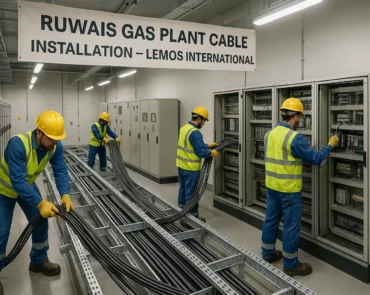
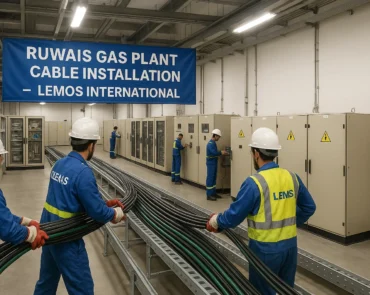
What is Challenge for client?
Lemos International successfully executed the installation of cable trays and wiring for the compressor control systems at the Ruwais Gas Plant, operated by GASCO. The project involved the installation of 12 kilometers of multicore control cables, termination and testing of loops to marshalling panels, and commissioning of Motor Control Center (MCC) panels. Our meticulous planning and execution ensured that all systems were energized on time and passed rigorous inspections with flying colors.
Our scope of work included:
- Cable Tray Installation: Designed and installed cable tray systems to support the extensive network of multicore control cables.
- Wiring Execution: Installed and terminated 12km of multicore control cables, ensuring accurate connections to field devices and marshalling panels.
- Loop Testing: Conducted comprehensive loop testing to verify signal integrity and functionality between field instruments and control systems.
- MCC Panel Commissioning: Commissioned MCC panels to ensure seamless integration with the plant’s electrical and control infrastructure.
- QA/QC Compliance: Performed rigorous quality checks and documentation to meet GASCO’s stringent standards.
The project was completed with precision, adhering to international standards and delivering a reliable, efficient, and compliant solution for the gas plant.
Key Features of the Project
Extensive Cable Tray Network
- Designed and installed robust cable tray systems capable of supporting 12km of multicore control cables.
- Ensured proper alignment, spacing, and grounding of trays to prevent signal interference and ensure long-term durability.
Multicore Cable Installation
- Laid and terminated 12km of multicore control cables, connecting field devices such as sensors, transmitters, and actuators to marshalling panels.
- Employed skilled technicians trained in cable pulling, routing, and termination to ensure accuracy and reliability.
Precision Loop Testing
- Conducted detailed loop testing using advanced diagnostic tools to verify signal transmission and system functionality.
- Documented test results meticulously, ensuring traceability and compliance with regulatory requirements.
MCC Panel Commissioning
- Commissioned MCC panels to integrate motor controls with the plant’s Distributed Control System (DCS), enabling centralized monitoring and operation.
- Verified panel performance through functional tests and load simulations to ensure operational readiness.
On-Time Energization
- Successfully energized all systems within the agreed timeline, allowing GASCO to proceed with plant operations without delays.
- Passed all inspections with zero non-conformities, reflecting our commitment to quality and precision.