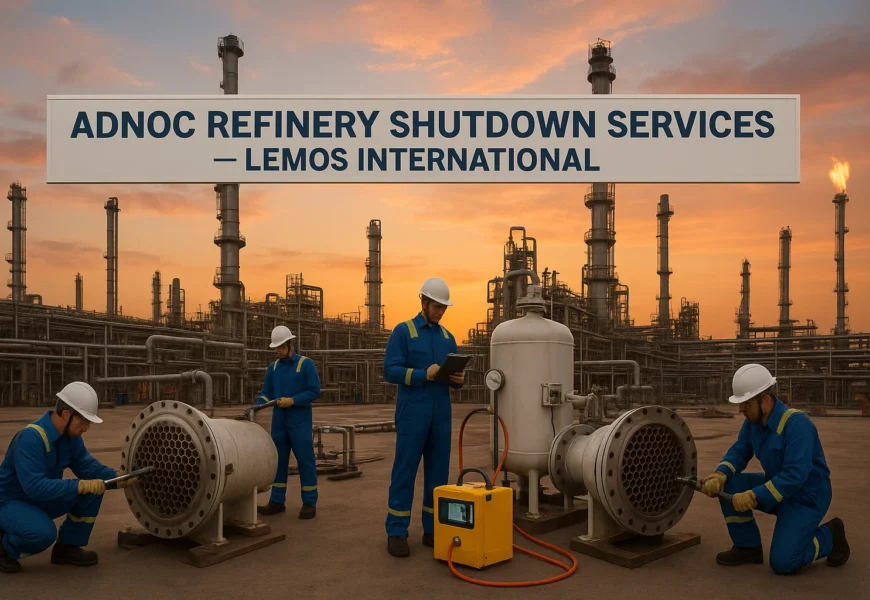
Project Details
- Plant Shutdown Services
- 10th October 2022
- ADNOC Refining
- Shutdown, Mechanical Maintenance
Project Description
Lemos International successfully executed a comprehensive plant shutdown and mechanical maintenance project for ADNOC Refining at their Ruwais refinery in Abu Dhabi. The project involved the overhauling of critical equipment, including heat exchangers and pressure vessels, as well as specialized tasks such as bolt torqueing and helium leak testing. Our team delivered exceptional results within a tight timeframe, ensuring minimal downtime and maximum operational efficiency for the refinery.
Our scope of work included:
- Shutdown Execution: Planning and execution of the plant shutdown, encompassing all mechanical maintenance activities.
- Heat Exchanger Overhauling: Disassembly, cleaning, inspection, and reassembly of heat exchangers to restore optimal performance.
- Pressure Vessel Maintenance: Inspection, repair, and recertification of pressure vessels to ensure compliance with safety standards.
- Bolt Torqueing: Precision tightening of flange bolts using hydraulic torqueing tools to achieve uniform stress distribution and prevent leaks.
- Helium Leak Testing: Conducted advanced helium leak testing to identify and rectify potential leaks in critical systems, ensuring safe and reliable operations.
The project was completed with meticulous attention to quality, safety, and regulatory compliance, reinforcing our reputation as a trusted partner for industrial maintenance projects.
Key Features of the Project
Comprehensive Shutdown Planning
- Developed a detailed shutdown schedule that minimized downtime while ensuring all critical maintenance tasks were completed on time.
- Coordinated closely with ADNOC’s operations team to align activities with refinery production schedules.
Heat Exchanger Overhauling
- Performed thorough inspections to identify wear and tear, corrosion, and other issues affecting performance.
- Utilized advanced cleaning techniques to remove fouling and deposits, restoring heat transfer efficiency.
- Reassembled units with precision gasket installations and bolt torqueing to eliminate leaks.
Pressure Vessel Maintenance
- Conducted non-destructive testing (NDT) to assess the structural integrity of pressure vessels.
- Repaired welds and replaced damaged components as needed, ensuring compliance with ASME and API standards.
- Recertified vessels through rigorous hydrostatic testing and documentation.
Advanced Helium Leak Testing
- Employed state-of-the-art helium leak detection technology to identify even the smallest leaks in flanges, valves, and piping systems.
- Rectified identified leaks promptly, ensuring zero tolerance for potential hazards.
Precision Bolt Torqueing
- Used calibrated hydraulic torqueing tools to achieve precise bolt tension, reducing the risk of joint failure and improving system reliability.
- Documented torque values for all connections to ensure traceability and compliance with QA/QC requirements.
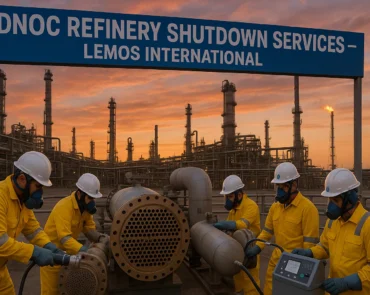

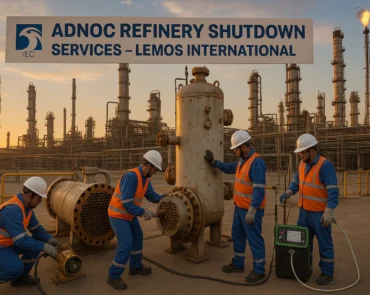
What is Challenge for client?
Challenge 1: Tight Timeline
The shutdown had to be completed within a strict 45-day window to avoid impacting refinery operations.
Solution:
We developed a highly efficient work plan, dividing tasks into parallel streams and deploying additional skilled manpower where necessary. By optimizing resource allocation and working extended shifts when required, we completed the shutdown in just 41 days, exceeding expectations.
Challenge 2: Ensuring Zero Defects During QA/QC Inspections
Achieving full approval of QA/QC documentation required flawless execution and adherence to stringent quality standards.
Solution:
We implemented a robust quality assurance program, conducting real-time inspections and mock audits throughout the project. Every task was meticulously documented, and all findings were addressed immediately. This proactive approach ensured that all QA/QC documentation was approved without delays or rework.
Challenge 3: Managing Safety Risks in a High-Hazard Environment
Working in an operational refinery posed significant safety risks, particularly during tasks such as bolt torqueing and helium leak testing.
Solution:
Our team adhered to strict HSE protocols, conducting daily toolbox talks and implementing permit-to-work systems for all high-risk activities. We also deployed gas detectors and personal protective equipment (PPE) to safeguard workers from potential hazards.
Outcome & Client Satisfaction
The successful completion of the ADNOC Refinery shutdown underscores Lemos International’s ability to deliver complex industrial maintenance projects under challenging conditions. Key achievements include:
- Early Completion: The shutdown was completed four days ahead of schedule, allowing the refinery to resume operations earlier than planned.
- Enhanced Equipment Performance: Overhauled heat exchangers and pressure vessels demonstrated improved efficiency and reliability post-maintenance.
- Zero Leaks or Failures: Helium leak testing and precision bolt torqueing ensured no leaks or failures were reported after recommissioning.
- Full Regulatory Compliance: All QA/QC documentation was approved by ADNOC and relevant authorities, reflecting our commitment to quality and safety.
ADNOC Refining expressed high satisfaction with the outcome, praising our team’s professionalism, technical expertise, and dedication to delivering exceptional results.
Why Choose Lemos International?
At Lemos International, we specialize in providing world-class shutdown and mechanical maintenance services for the oil and gas, petrochemical, and industrial sectors. Our core strengths include:
- Proven Expertise in Shutdowns: With extensive experience in managing large-scale shutdowns, we understand the unique challenges and requirements of these projects.
- Commitment to Safety: Safety is our top priority, and we adhere to the highest HSE standards to protect our workforce and client assets.
- Focus on Quality: We leverage advanced technologies and rigorous QA/QC processes to ensure every task meets or exceeds industry standards.
- Timely Delivery: Our efficient planning and execution strategies enable us to complete projects on or ahead of schedule, minimizing downtime and maximizing productivity.